Open die forging is a manufacturing process used to shape metal alloys into custom parts and components, which are used across a wide range of industries including aerospace, automotive, construction, mining, and energy. Also known as smith forging, free forging or hand forging, open die forging is a common technique for producing large, non-uniform parts that cannot be produced through other manufacturing processes.
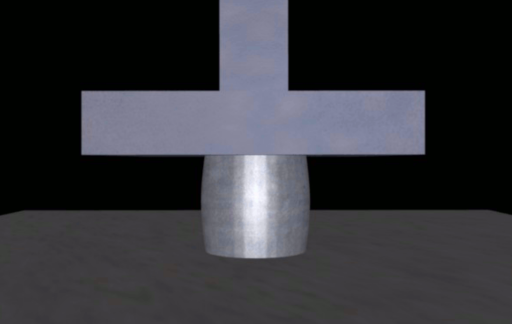
The process of open die forging involves heating a metal alloy to its plastic state, then shaping it into a desired form either manually or by using a hydraulic press. The metal is hammered, pounded, squeezed or rolled into shape under high pressure, producing high-strength parts that have a dense microstructure. Open die forging can be performed on virtually any type of metal or alloy, including carbon and stainless steels, aluminum, titanium, brass and nickel-based alloys.
Open Die Forging Process
The open die forging process can produce a range of shapes, including round bar, flat bar, disc, ring, cylinder, and plunger. The process typically involves multiple operations, including preheating, upsetting, rough forging, and finish forging.
Preheating: Before forging, the metal is heated to a specific temperature to make it easier to shape. Depending on the metal and its alloy content, preheating temperatures can range from 300 to 1200 degrees Fahrenheit.
Upsetting: This process involves increasing the thickness of the metal while decreasing its length. It involves heating an area of the metal over a short length and then striking it with a series of hammers, presses or other tools. The result is a block or blank that is then ready for further forging.
Rough Forging: Rough forging involves forming the block into a specific shape by compressing it under high pressure. A hydraulic press is often used to apply pressure from multiple directions to shape the metal into the desired form.
Finish Forging: This final operation involves forming the metal into its final shape, often with more precision than rough forging. Depending on the shape of the final product, tools such as hammers or presses may be used to apply pressure to specific areas of the metal.
Open Die Forged Cylinder Plunger
One example of a part that can be manufactured using open die forging is a cylinder plunger. Cylinders are used in many applications, such as hydraulic systems, where they require high strength and durability. Open die forging enables the production of large, non-uniform cylinders with enhanced mechanical properties.
The forging of a cylinder plunger requires multiple operations, including heating, upsetting, and finish forging. The starting material is heated to a specific temperature and then upset to increase the thickness of the metal while decreasing its length. The pre-formed blank is then further forged into its final shape, with multiple finish forging operations applied to create the desired dimensions and shape.
Benefits of Open Die Forging
Open die forging offers several benefits over other manufacturing processes, including:
- The ability to produce large, non-uniform parts.
- Enhanced mechanical properties due to fine grain structure.
- Improved strength and impact resistance compared to cast parts.
- Greater flexibility in design and production.
- Better control over cost and delivery time.
Conclusion
In summary, open die forging is a versatile manufacturing process that can produce high-strength parts and components for a wide range of applications. The process involves multiple stages of heating, shaping, and finishing, enabling the production of large, non-uniform parts with enhanced mechanical properties. Cylinder plungers are one example of a part that can be produced using open die forging, offering superior strength and durability compared to cast parts. With its many benefits and flexible design options, open die forging is a popular choice for manufacturers across multiple industries.