Flanges play an integral role in piping systems as they are used to connect pipes, valves, pumps, and other components to create a network. These flanges come in various types and materials to meet the unique needs of different applications. Forged steel flanges, in particular, are highly sought after due to their strength, durability, and resistance to extreme conditions.
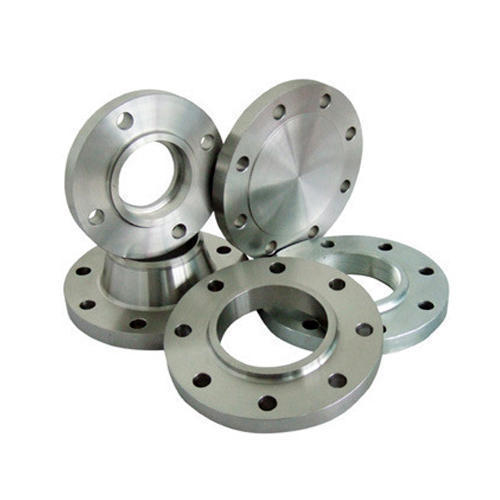
If you're in the market for forged steel flanges, it's essential to understand the two main types – open die forgings and seamless rolled rings. In this blog, we'll delve into open die forged flanges, types, and connections.
What Are Open Die Forged Flanges?
Open die forging is a forging process that involves hammering or pressing the heated metal between two flat or contoured dies. Open die forging creates products that require high strength, ductility, and resistance to corrosion, making them ideal for high-pressure applications like pipelines and oil rigs.
Open die forged flanges are manufactured by heating steel billets, hammering or pressing them between two flat dies, creating a rough shape. The flanges are then finished using machining processes, such as turning or milling, to achieve the final dimensions and tolerances required. The rough shape created by the open die forging process allows for additional customization of the flange, including its size and shape, making it a popular choice for bespoke applications.
Types of Open Die Forged Flanges
The open die forging process allows for a wide range of flange shapes, each designed for specific applications or connections. Here are some of the most common open die forged flange types:
- Blind flanges – Blind flanges are used to close off a pipe or a valve. They have no holes, and their design allows for easy sealing of the opening.
- Lap joint flanges – Lap joint flanges consist of two components – a stub end and a flange designed to slide over the pipe end. This type of flange is commonly used in piping systems that require regular maintenance and cleaning.
- Slip-on flanges – Slip-on flanges are designed to slide over the pipe end and are welded in place. They are commonly used in low-pressure applications.
- Weld neck flanges – Weld neck flanges are designed to be butt-welded with the pipe. They have a tapered hub that helps reduce stress and provide a consistent flow rate.
Connections for Open Die Forged Flanges
The connection between the flange and the pipe is crucial for the performance and durability of the piping system. Here are some of the most common connections for open die forged flanges:
- Threaded connections – Threaded connections involve threading the end of the pipe to match the threads on the flange. They are used in low-pressure applications and are generally not recommended for high-pressure systems.
- Welded connections – Welded connections are the most common type of flange connection. They involve welding the pipe to the flange, creating a strong, leak-proof connection.
- Bolted connections – Bolted connections involve the use of bolts and nuts to attach the flange to the pipe. They are a popular choice for low-pressure and non-critical applications.
Conclusion
Open die forged flanges are an excellent choice for piping systems that require high strength, ductility, and resistance to corrosion. The open die forging process allows for a wide range of flange shapes, each designed for specific applications or connections. When selecting an open die forged flange, it's essential to consider both the type of flange and the connection method to ensure a secure, leak-free connection.
At (company name removed), we specialize in open die forged flanges for a wide range of industries, including oil and gas, power generation, and aerospace. Contact us today for more information on our open die forged flange solutions.