The machine in question was commissioned in the year 2013 and had been running for a considerable period. After a long run, the sealing fins of the rotor and guide blade carriers (GBC) were found worn out. This was a significant problem as the rotor's sealing fins are crucial components that help maintain the proper clearances between the rotor and stator. If they are worn out or damaged, it could lead to rubbing and damage to the turbine's components.
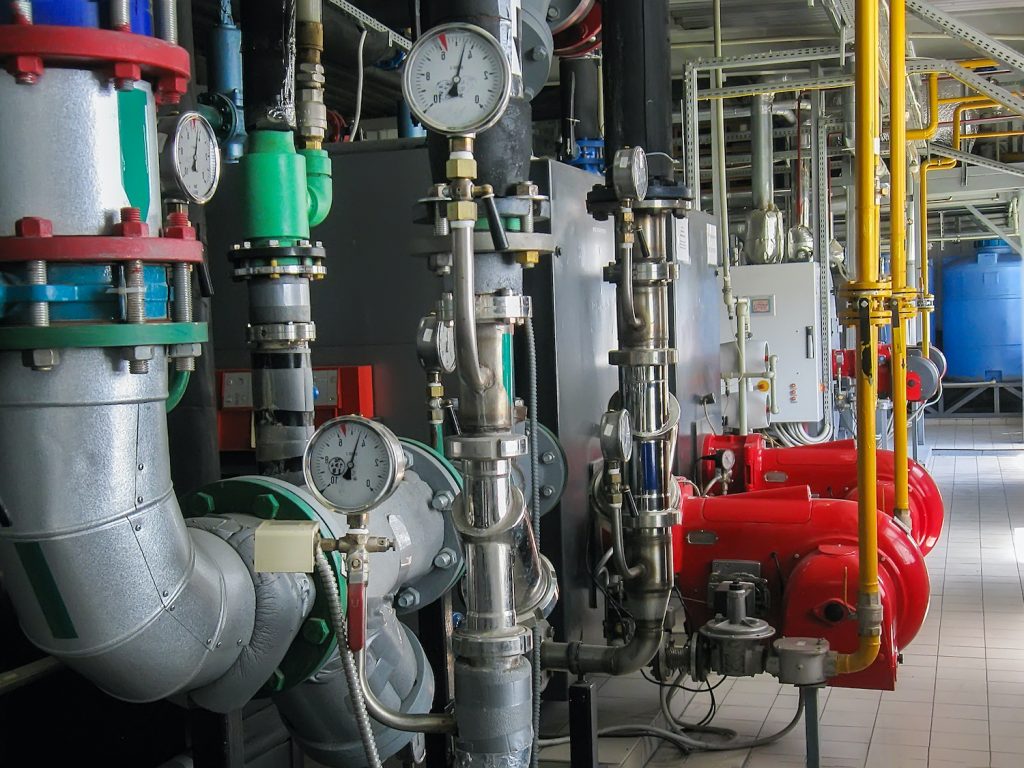
To address this problem, the complete set of sealing fins of the rotor had to be replaced during the overhauling process. The replacement rotor fins had to be of the same quality as the original ones, and the repair procedure had to be meticulously planned and executed to ensure a perfect fit. Corrective measures had to be taken to prevent the same issue from recurring in the future.
One of the critical factors in ensuring a perfect rotor fit is the quality of the forging process. In this case, the steam turbine rotor was produced using a free die forged manufacturing process, which involves forcing the metal into a die without the use of an enclosed impression. The process produces a superior quality of the rotor, with high levels of resistance to wear and tear. The use of a free die forging process guarantees the highest level of precision, strength, and durability. The rotor produced via this process has excellent mechanical properties, including resilience and torsional strength.
During the overhauling process, it was found that the rotor was bowed, making the replacement of the sealing fins a considerably more complex process. The bowing of the rotor is a relatively common occurrence in steam turbines and is usually caused by thermal or mechanical stresses. To rectify this, the rotor had to be straightened with specialized equipment, subjected to rigorous tests to ensure it was perfectly balanced, and returned to its original shape before the sealing fins were replaced.
In conclusion, the overhauling of a steam turbine is a complex process that requires a detailed understanding of the machine's components and their interdependencies. The replacement of the sealing fins of the rotor in a 32MW double extraction condensing steam turbine required a thorough understanding of the free die forging process, the effects of thermal and mechanical stresses on turbine components, and the use of specialized equipment to rectify the problem. The successful overhaul of the steam turbine rotor has ensured that the machine remains in excellent working condition, providing reliable power generation for years to come.